Problem jest wtedy, kiedy problemów nie ma
– Według nas pod pojęciem filozofii lean, którą stosujemy w browarze, kryje się sytuacja, gdzie właściwe osoby spotykają się we właściwym miejscu o właściwym czasie i rozmawiają o właściwych rozwiązaniach problemów, które wystąpiły – mówi Piotr Zając, dyrektor Browaru Kasztelan w Sierpcu.
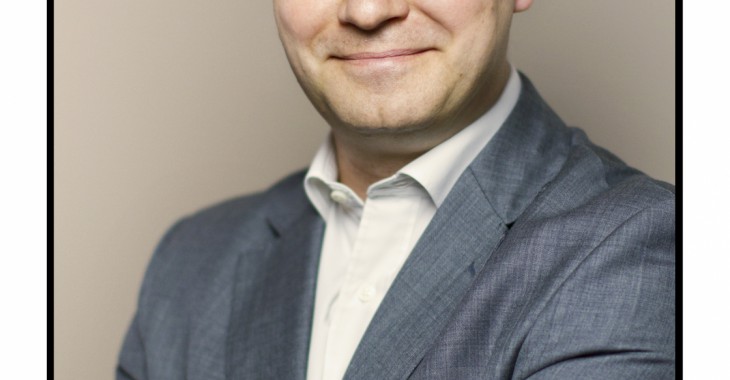
Zwiększenie mocy produkcyjnych, linia puszkowa oraz nowa, bardziej wydajna energetycznie warzelnia z filtrem zaciernym. Skąd potrzeba tak dużych zmian w Browarze w Sierpcu?
Nasze marki stają się coraz silniejsze i coraz bardziej popularne. To właśnie wzrost popularności marki Kasztelan, warzonej w tym browarze, był bezpośrednią przyczyną inwestycji.
Drugim powodem był fakt, że Browar w Sierpcu do tej pory nie miał linii puszkowej. Rozbudowując moce w Sierpcu, dodaliśmy linię puszkową, która mieści się w osobnej, nowej hali. Wyłączyliśmy też starą warzelnię, która była już nieefektywna energetycznie.
Browar po zakończeniu inwestycji może warzyć 2,5 raza więcej piwa niż wcześniej.
Czy te dodane moce są już w pełni wykorzystywane?
Na razie w około 70%. W pełni, zgodnie z naszymi planami, powinny być wykorzystywane od kwietnia – maja.
Jeśli chodzi o browar w Sierpcu, dotąd w ślad za rosnącą popularnością naszych marek nie szły żadne duże inwestycje związane ze zwiększeniem mocy produkcyjnych.
Jak browar w Sierpcu wygląda teraz, w porównaniu do pozostałych browarów Carlsberga?
Browar Kasztelan nadal jest stosunkowo mały. Jeżeli chodzi o moce produkcyjne, jest porównywalny z naszym Browarem Bosman w Szczecinie i o połowę mniejszy od Browaru Okocim w Brzesku.
Czy zmiany, jakie zaszły w browarze, wpłynęły na pracę ludzi?
Inwestycje dały duży zastrzyk wiedzy dotyczącej nowych trendów jeżeli chodzi o wyposażenie, systemy kontroli czy automatyki. Kwalifikacje naszych ludzi związanych z utrzymaniem ruchu na pewno się podniosły. Mieliśmy całą serię szkoleń prowadzonych przez producentów maszyn i urządzeń. Wszystko po to, żeby przy okazji tak dużego projektu podnosić umiejętności naszych pracowników. Zmieniliśmy też kilka systemów sterowania, które funkcjonują w browarze, a w ślad za tym poszły odpowiednie szkolenia załogi.
Wspominał pan o wyłączeniu starej warzelni i podniesieniu efektywności produkcji. Jak udało się zmniejszyć zapotrzebowanie na energię?
Generalnie są tu dwa elementy. Pierwszym jest sam fakt, iż mówimy tutaj o nowej warzelni, nowych materiałach izolacyjnych i zmniejszonych stratach ciepła w obrębie tego działu. Poprzednia warzelnia była modernizowana w latach 90. i materiały izolacyjne używane do jej budowy i przebudowy zamortyzowały się i wymagały coraz częstszego uzupełniania. Drugim elementem jest to, że rozlew piwa do puszek jest mniej energochłonna niż do butelek.
Położyliśmy również nacisk na wykorzystanie ciepła odpadowego. Kotłownia, która także była modernizowana, wykorzystuje je po to, aby dogrzewać magazyn. Część tego ciepła jest używana w słodowni do wstępnego podsuszania słodu, tam, gdzie ilość dostarczanego ciepła zależy od temperatur na zewnątrz. To są te rozwiązania, które pozwoliły nam myśleć nie tylko o rozbudowie browaru, ale również byciu bardziej przyjaznym dla lokalnej społeczności i środowiska.
W wielu branżach przemysłu wdrażane są koncepcje zarządzania takie jak lean. Czy w Browarze Kasztelan również używacie tego typu rozwiązań?
Również i my czerpiemy inspiracje z innych branż. Muszę tutaj wspomnieć, że prekursorem całej filozofii w naszej grupie jest koleżanka Dagmara Gutowska, która zdobywała pierwsze szlify w Toyocie w Polsce. W tej chwili Dagmara pracuje w Wielkiej Brytanii, gdzie z sukcesem wprowadza lean w innych browarach Grupy Carlsberg w Europie.
Można wiele mówić o tym, czym jest lean. My pod tym pojęciem rozumiemy dobre zarządzenie i to, że właściwe osoby spotykają się we właściwym miejscu o właściwym czasie i rozmawiają o właściwych rozwiązaniach problemów, które wystąpiły. Dyskutują o małych problemach, zanim staną się wielkimi, z poważnymi konsekwencjami środowiskowymi czy finansowymi. Takie rozumienie lean staramy się promować wśród naszych pracowników.
Jak to wygląda w praktyce?
Mamy wdrożony system spotkań. Poczynając od godziny 8 rano manager danego działu spotyka się ze swoimi pracownikami. Struktura takiego spotkania jest bardzo wyraźnie określona. Zaczyna się od spraw ludzkich, związanych chociażby z bezpieczeństwem pracy i sytuacjami potencjalnie wypadkowymi. Następnie przechodzimy przez wskaźniki dotyczące jakości i tego, czy pojawiły się jakieś odchylenia, na które powinniśmy zwrócić uwagę. Wreszcie poruszane są kwestie serwisów, jakie dostarczamy naszym klientom wewnętrznym i tego, czy pojawiły się czynniki, które ten serwis zakłóciły i czy wywiązaliśmy się ze swoich zobowiązań dostarczając kolegom z innego działu to, na co czekali. Przechodzimy w końcu do kwestii czy zrobiliśmy wszytko po założonych kosztach, czy straty opakowań i piwa były nie większe niż te, które postawiliśmy sobie za cel, czy zużycie mediów na maszynach było takie, jakie powinno być.
W ten sposób, kontrolując bezpieczeństwo, jakość, serwis i koszty odbywamy spotkanie trwające około 20 minut. Później przechodzimy przez bieżące problemy, które były zidentyfikowane na poprzednich spotkaniach. Do tych problemów przypisane są konkretnie osoby i odpowiedzialności. Kontrolujemy, czy dana kwestia jest w fazie planowania, wykonywania, lub weryfikujemy już rozwiązane trudności upewniając się, że sprawa została doprowadzona do końca i nie wróci do nas jak bumerang w innej postaci.
Podobne spotkania organizowane są na poszczególnych działach produkcyjnych, aż w końcu o godzinie 11 mamy półgodzinne spotkanie operacyjne na moim poziomie. Managerowie poszczególnych działów zdają relacje dokładnie według tej samej procedury. Analizujemy wtedy też problemy pod kątem tego, czy nie jest potrzebna np. moja interwencja.
Czy ostatnie inwestycje wydłużyły listę problemów, czy ją skróciły?
Początki to zawsze więcej trudności, zawsze jest jakaś krzywa uczenia się. Lista problemów wynika najczęściej z czterech podstawowych rzeczy: ludzi, maszyn, metod pracy, których się ciągle uczymy, albo materiałów, jakich do tej pory nie mieliśmy, a nagle zaczynamy mieć, np. puszki.
W związku z tym, że zwiększyła się skala produkcji i powstała nowa linia, zwiększyło się również zatrudnienie. Sam fakt uczenia się przez nowych pracowników naturalnie generował problemy, które rozwiązujemy na bieżąco. Moim zdaniem najważniejszą rzeczą jest spisanie tych problemów i systematyczne podchodzenie do ich rozwiązywania. Wspomniana przeze mnie wcześniej Dagmara Gutowska zawsze powtarza, że problem jest wtedy, kiedy problemów nie ma, bo wówczas mamy złudne poczucie komfortu. Wydaje się, że wszystko funkcjonuje, ale praktycy wiedzą, że zawsze jest „coś”, pytanie tylko czy zwracana jest na to „coś” odpowiednia uwaga.
Rozmawiał Adam Wita
SIEDZIMY NA JEDNEJ GAŁĘZI Piotr Zając: Uważam, że mówienie źle o innych producentach piwa to grzech, który jest często popełniany w Polsce. Rozumiem powody, wynikają z tego, iż jedni chcą się odróżnić od drugich i wybierają drogę deprecjonowania innych, żeby uwiarygodnić siebie jako lepszych. Takie zachowania uważam za „antykategoryjne”. Podcinają one gałąź, na której my wszyscy, piwowarzy, siedzimy. To jest grzech, z którego nie zamierzam w żaden sposób rozgrzeszać i będę z nim walczył. |
Wywiad został opublikowany w numerze 1/2015 magazynu Agro Przemysł
Fot. Carlsberg Polska