Poprawa efektywności produkcji dzięki Lean Manufacturing
Lean Manufacturing to bodajże najpopularniejszy i najefektywniejszy sposób na poprawę efektywności, redukcję kosztów i skrócenie czasu realizacji produkcji. Lean powstał i rozwinął się w Japonii, a firmą, która jest liderem, pionierem i pierwowzorem Lean jest Toyota, ale jego korzeni możemy dopatrywać się (100 lat temu) w fabryce Henrego Forda.
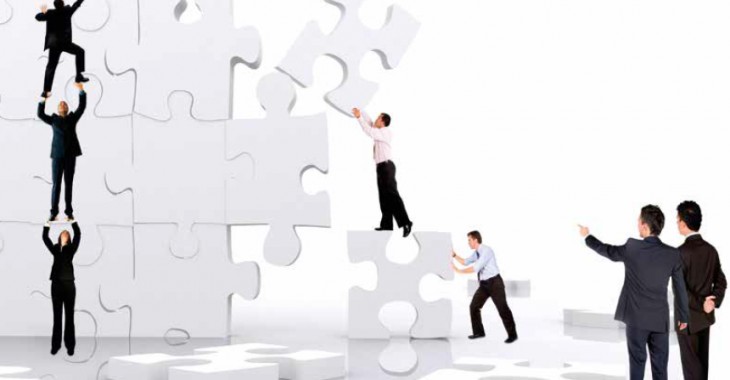
Na czym polega Lean?
Lean to usprawnianie przepływu poprzez eliminację marnotrawstwa. Marnotrawstwa zostały zdefiniowane
przez Taichi Ohno (uważanego za twórcę Toyota Production System) i są nimi:
• Transport – przemieszczanie materiału. Transportu całkowicie wyeliminować się nie da, ale należy go minimalizować,
• Zapasy – nadmierna ilość surowca, produkcji w toku, wyrobów gotowych,
• Nadmierny ruch – marnotrawstwo wynikające z braku ergonomii i złej organizacji stanowisk pracy,
• Oczekiwanie np. na dostarczenie materiałów, na usunięcie awarii, na zakończenie przezbrojenia,
• Nadprodukcja – produkowanie za dużo, za szybko lub za wcześnie w stosunku do potrzeb,
• Zbędne przetwarzanie – wykonywanie czynności, które w ogóle nie powinny być wykonywane,
• Braki i błędy – produkty bądź półprodukty, które po procesie nie spełniają wymagań klienta i które
należy poprawić lub wykonać ponownie.
Do powyższych marnotrawstw dodaję się jeszcze zwykle niewykorzystany potencjał – np. niekorzystanie z wiedzy i kreatywności pracowników.
Marnotrawstwa są objawami problemów występujących w organizacji i żeby je wyeliminować trzeba zidentyfikować i usunąć ich przyczyny.
Usprawnianie przepływu to z kolei sprawianie, że przepływ materiału będzie następował bez zbędnych zatrzymań i czas przejścia przez zakład od dostawy surowca do wysyłki do Klienta będzie możliwie jak
najkrótszy.
Narzędzia Lean
W przemyśle spożywczym Lean w dużym uproszczeniu sprowadza się poprawiania stabilności i dostępności procesów i zmniejszania poziomu zapasów w całym strumieniu.
Z tego powodu szczególnie ważnymi narzędziami Lean w tej branży są:
• poziomowany plan produkcyjny w połączeniu z supermarketem wyrobów gotowych, pozwalający na możliwie równomierne obciążenie pracą i sensowną w punktu widzenia produkcji kolejność zleceń, przy możliwie małych zapasach i dostępności wyrobów gotowych dla Klienta,
• TPM, (Total Productive Maintenance), czyli całkowicie produktywne utrzymanie ruchu to narzędzie, którego celem jest zero awarii i zero problemów wynikających z pracy maszyn i urządzeń,
• SMED (Single Minute Exchange of Die), a więc skracanie czasów przezbrojeń.
(...)
Poprawne wdrożenie i utrzymanie powyżej zaproponowanych
rozwiązań powoduje:
• wysoką dostępność wyrobów dla klienta,
• krótki czas realizacji zamówień,
• niski poziom zapasów,
• niższe zaangażowanie kapitału, a więc poprawęc cash flow,
• wzrost produktywność,
• obniżenie kosztów produkcji,
• mniejsze zapotrzebowanie na powierzchnię magazynową,
• stabilniejszą i spokojniejszą produkcję.
Zdjęcie: www.photogenica.pl
Artykuł został opublikowany w nr 1/2014 magazynu "Agro Przemysł"